Many people dream of building a house from the ground up, but the crucial process of estimate building materials for home construction is hidden beneath the enthusiasm. This crucial phase affects the project’s total cost as well as its quality. In addition to assisting in the creation of a reasonable budget, precise estimates guarantee that construction proceeds without hiccups and that resources are available when required.
Estimating errors may result in expensive delays, resource waste, and overspending. We provide you with the information you need to successfully oversee your home building project by guiding you through the material estimation process in this guide.
Knowing the Fundamentals: Why Building Material Estimation Is Crucial for Home Construction
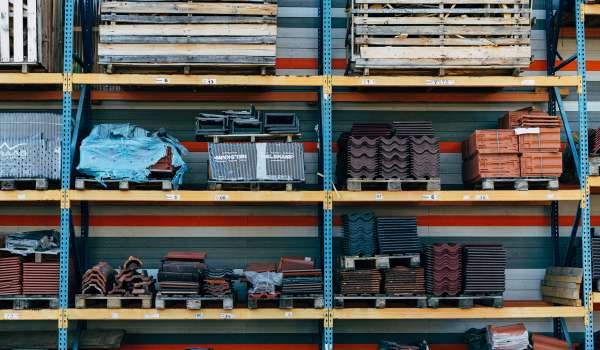
Building material estimation is the cornerstone of a successful construction and involves more than simply math calculations. Every component, from timber to nails, has an impact on the project duration and the total budget. Accurate estimates help you stay within the project’s scope by preventing shortages and overpaying. By reducing waste and promoting consistency, this foundation enables your idea to materialize without continual interruptions.
Budgeting: The Effect of Material Estimation on the Total Cost of Building a Home
In Estimate Building Materials for Home Construction, understanding each dollar’s purpose is essential, going beyond just the final budget. A detailed assessment of materials provides a clear breakdown of expected costs, allowing for strategic fund allocation at each stage of the project. By determining the materials required for each phase, you achieve a balance between essential needs and finishing touches, making informed choices from the outset and avoiding unnecessary compromises down the line.
Deconstructing the Home Building Process: The Role of Every Material
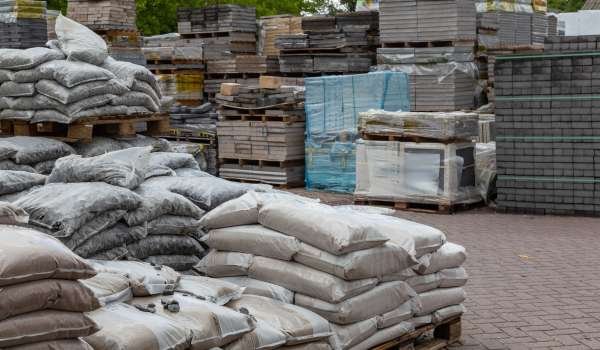
Each material has a specific role to play in the building schedule. Delays may be avoided by being aware of when supplies are required, whether it be for the initial roofing, framing, or finishing phases. By dissecting the procedure, you may also schedule delivery at different times, lowering the possibility of items lying around undisturbed, which might result in damage or storage problems.
Knowing Floor Plans and Blueprints: The Basis for Precise Estimation
Floor plans and blueprints serve as the maps that direct the estimate of materials. You may precisely estimate the amount of each material needed by examining plan details and measurements. For instance, drywall requirements are determined by the height and length of the wall, while shingle requirements are influenced by the area and pitch of the roof. You can picture every space and guarantee precise estimations if you are familiar with these blueprints.
Materials for Site Preparation: Estimating Clearing, Excavating, and Grading Costs
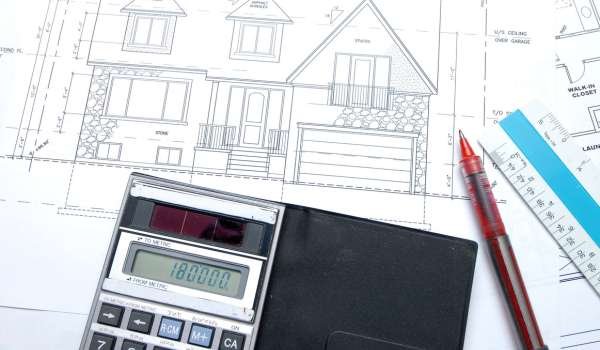
The first physical phase is site preparation, which requires a specific set of supplies, such as sand and gravel for leveling and protective covers for surrounding buildings. The natural slope of the ground, the kind of soil, and any required filling or removal must all be taken into account when estimating these materials. A solid foundation is ensured by precise site preparation, which sets the tone for the whole undertaking.
Calculating Concrete, Rebar, and Other Necessary Materials for a Foundation
The foundation acts as the anchor for the house, and its components—mainly rebar and concrete—are crucial to its structural soundness. In order to determine the proper quantity of concrete and steel reinforcement, it is necessary to measure the size and depth of the foundation. The long-term durability of the house is impacted by every choice, from kind to thickness, thus accurate assessment is essential.
Choosing the Right Amount of Lumber, Nails, and Fasteners for the Framing
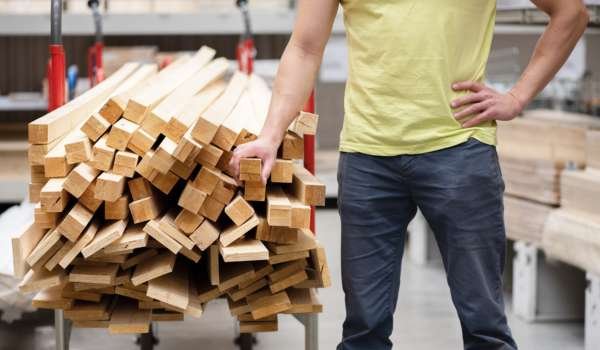
The framework of your house is its framing. The quantity of timber and connections required, as well as the arrangement, are determined by the number of studs, joists, and beams. Calculating the structure for each room makes estimating these materials a geometry exercise. Accurate framing calculations provide the whole building strong support without wasting resources.
Roofing Fundamentals: Determining the Size of Your Roof’s Shingles, Underlayment, and Flashing
Your home’s roof protects it from the weather, and high-quality materials are essential to its longevity. Roof size and slope must be taken into consideration in order to estimate shingles, underlayment, and flashing accurately. This eliminates the possibility of a shortfall during installation and guarantees that the roof is completely covered and free of any weak spots that can allow leaks.
Wall Materials: Calculating the Requirements for Sheathing, Insulation, and Drywall
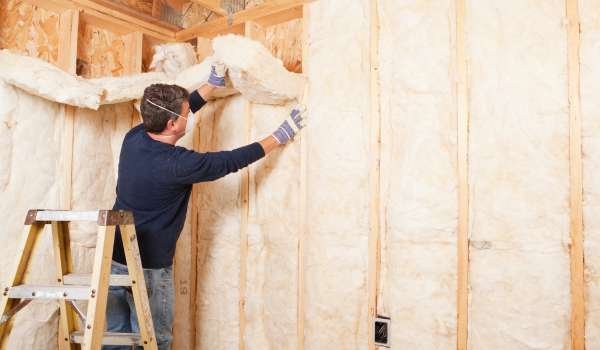
Walls provide soundproofing, insulation, and protection in addition to being obstacles. Sheathing, insulation, and drywall estimates must be made room-by-room while accounting for wall width and height. Accurate calculations guarantee that walls are level and free of gaps that might jeopardize sound isolation or temperature regulation.
Siding and External Finishes: Selecting and Calculating the Amount of Siding Material
Siding improves the appearance of your house in addition to providing protection. The kind of siding—wood, fiber cement, or vinyl—affects installation requirements and cost. In order to guarantee accuracy in the procurement and installation of siding materials, it is necessary to measure the outside surface areas and take window and door openings into consideration.
Estimating Material Requirements for Various Sizes and Types of Windows and Doors

Doors and windows are important components in estimating building materials for home construction since they let in natural light and air. When estimating materials, the precise measurements and frame types of these holes must be taken into account. Accurate measurements guarantee that every point of entrance and departure fits perfectly with the wall construction, preventing material shortages or overbuying.
Plumbing Fundamentals: Calculating Fittings, Fixtures, and Piping for Each Room
One of the trickiest parts of building is plumbing. The layout of the house must be carefully examined when estimating the pipes, fittings, and fixtures for the kitchen, bathroom, and laundry rooms. Water flow and pipe requirements are affected by each sink, toilet, and shower. A plumbing system that is both functional and efficient is ensured by careful assessment.
Electrical Supplies: Calculating All of the Home’s Wires, Outlets, and Fixtures
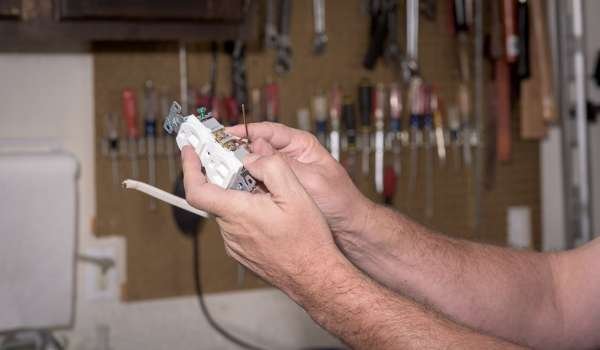
Every space needs wiring because electricity fuels everyday life. The purpose and layout of the space determine how long the wires, outlets, and light fixtures should be estimated. To provide enough power availability throughout the house, each outlet and switch has to match its intended use. This accuracy avoids surpluses or shortages that can make installation more difficult.
Calculating the Material Quantities for Hardwood, Carpet, Tile, or Laminate Flooring Needs
Although flooring options vary, precise material assessment never changes. The size of each room must be taken into account while choosing flooring, whether it be laminate, tile, carpet, or hardwood, to prevent surplus or shortage. Estimates for flooring not only guarantee uniformity in appearance but also make switching between various kinds of flooring easier.
How to Calculate the Appropriate Paint, Primers, and Brushes for Each Room
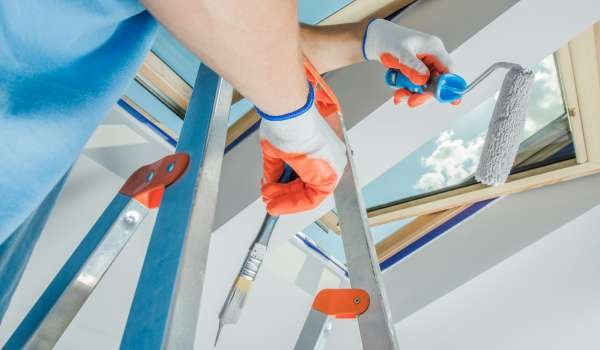
Paint is more than just a cosmetic option; it protects surfaces and seals walls. Calculating wall space, taking base color into consideration, and choosing primers and brushes are all part of paint estimation. The inside attractiveness of the house is improved by carefully balancing each coat to get the desired effect without wasting any.
Interior Fixtures: Calculating Closet Systems, Countertops, and Cabinetry
From kitchen cabinets to closets in bedrooms, interior fixtures provide both flair and functionality. Measuring the available area, taking access points into consideration, and selecting long-lasting finishes are all part of estimating these materials. Here, careful planning results in a unified interior without needless spending.
Outdoor Areas: Estimating Deck, Patio, and Landscaping Material Needs
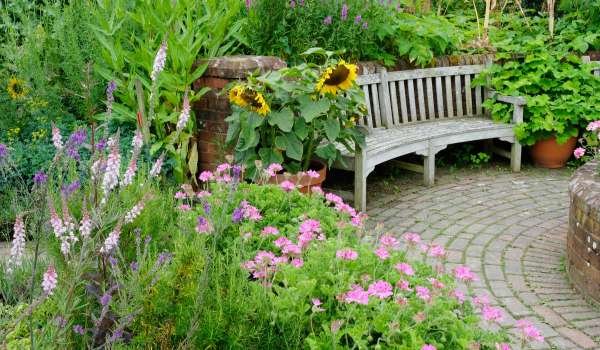
Outdoor spaces increase the value of your home and your living area. Determining the size of the yard and its planned usage is necessary when calculating the materials for patios, decks, and landscaping. Whether it’s a flower bed or a sidewalk, every exterior element improves the home’s utility and appeal, so careful material planning is essential.
Waste and Overages: Why It’s Frequently Necessary to Add 10% to 15% More Materials
It is unusual for construction to be without surprises. To account for errors, modifications, and unanticipated problems, add an additional 10% to 15% for supplies. This buffer allows for flexibility and peace of mind as work moves forward by preventing shortages from stopping development.
Sustainable Decisions: How to Calculate Eco-Friendly or Recycled Materials
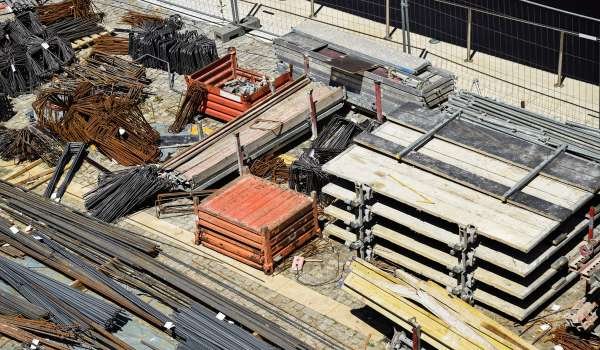
Sustainability is becoming more and more important in Estimate Building Materials Home Construction, which is why many builders choose recycled or eco-friendly materials. These sustainable choices may need further investigation for an accurate evaluation because of differences in cost and availability. Selecting environmentally friendly materials improves household health and lessens the project’s effect on the environment.
Making Calculations Easier with Estimation Tools and Apps
With tools that expedite computations for every aspect of building, technology streamlines the estimating process. These tools, which range from desktop software to mobile applications, provide an intuitive interface for entering measurements and material kinds, assisting you in making prompt and precise judgments.
How to Work with Suppliers to Get Precise Material Estimates and Savings
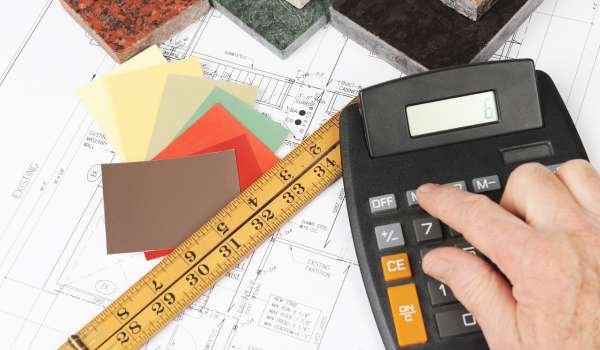
In the construction industry, suppliers are vital partners. Based on their inventory, they are able to give precise estimations and even provide discounts for larger orders. Developing a connection with suppliers saves time and money by securing trustworthy material sources.
Commonly Asked Questions about Building Material Estimation
Common queries when estimating construction materials range from selecting the appropriate material grades to modifying amounts for waste. By answering these frequently asked questions, you may have your questions answered and gain confidence in your building endeavors.
Learn More : How To Estimate Home Building Costs
Conclusion
Accurately estimate building materials for home construction is the cornerstone of a successful home building project. You’ll be ready for every stage of the project if you plan beforehand, have the appropriate equipment, and have some extra material on hand. With this method, an empty lot is turned into your ideal house, gradually turning your vision into a reality.